Article: Case Study #3
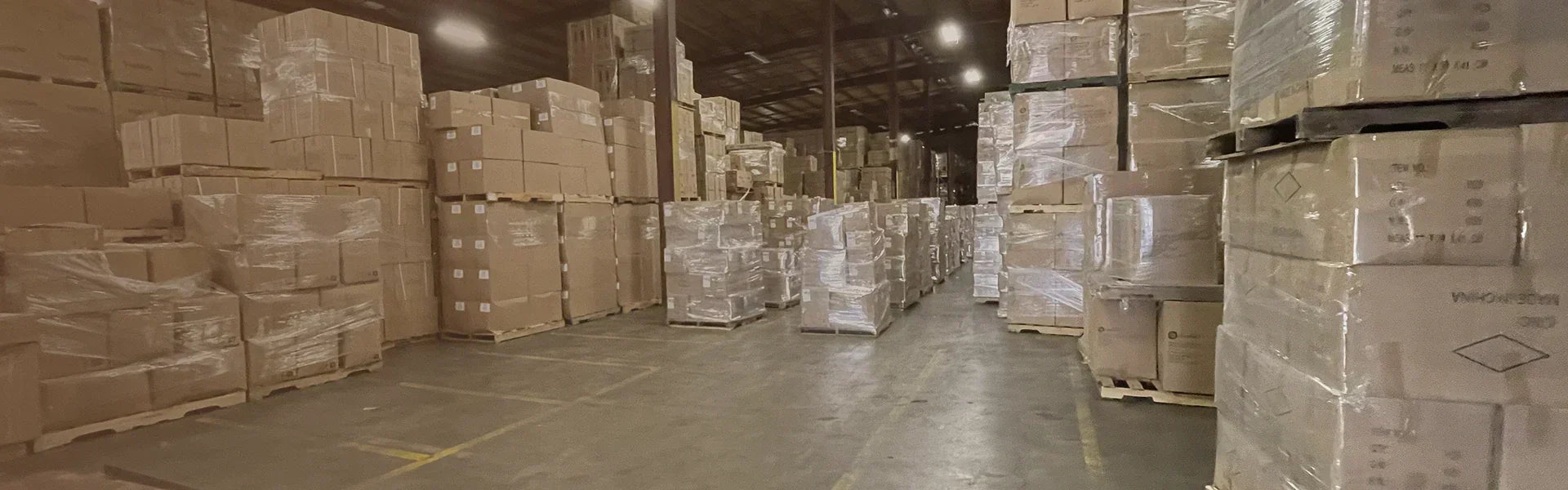
Case Study #3
Situation:
A leading plant-based foods manufacturer, specializing in non-dairy spreads, creams, and cheeses, is committed to environmentally responsible production. The company strives for a Zero-Waste-to-Landfill standard across all its manufacturing waste streams, embracing circular economy principles. One challenge area was the large volume of packaging materials involved in production: the company receives countless plastic tubs and lids from suppliers, which arrive in high-quality corrugated boxes. Once these packaging components are used on the production line, the empty corrugated boxes accumulate as waste. Their solution was to install conveyers and baling equipment which amounted to over $1 million in capital investment. However, this equipment requires frequent expensive maintenance and regularly breaks down and needs repair, negatively impacting production efforts. Relying solely on this traditional recycling method for this cardboard wasn’t the most sustainable option operationally, environmentally, or financially.
Task:
Develop a better solution which would improve financial, environmental, and operational impacts.
Action:
UsedCardboardBoxes (UCB) designed, negotiated, and managed a closed-loop program for their used packaging boxes, along with standard box reuse efforts.
Results:
Through this partnership, the client achieved notable improvements in sustainability and cost avoidance:
-
Tens of thousands of boxes reused monthly: The program now processes a high volume of used boxes every month (across the client’s participating facilities), converting what was previously just recyclable waste into reusable assets.Each of those boxes reused is one less new box that needs to be produced, reflecting a direct reduction in resource consumption.
-
Zero landfill maintained: Even when faced with equipment failure and other challenges, the company kept 100% of these corrugated boxes out of landfills. All usable boxes are either reused within the supply loop or managed by UCB for reuse elsewhere, reinforcing the client’s zero-waste-to-landfill achievement.
-
Strengthened circular economy: By sending packaging materials back to suppliers for reuse, the client has closed the loop in its supply chain. This not only diverts waste but also builds a stronger supplier partnership focused on sustainability. The continuous reuse cycle for boxes means less waste haulage and recycling processing, and a smaller environmental footprint for both the client and its suppliers.
-
Improved efficiency and oversight: The UCB program streamlined the client’s waste handling process for packaging. What used to be an overhead burden (managing piles of used boxes) is now an organized, efficient system. The client can track how many boxes are being reused versus recycled, gaining better insight into their sustainability metrics. Additionally, avoiding frequent baler downtime issues by having UCB manage overflow saved the client significant hassle and potential disposal costs.